HARDY Process Weighing Solutions with Unique Features
B+L Industrial Measurements has since 2005 been the authorized sales and service partner of the US-based manufacturer Hardy Process Solutions for the European market.
Headquartered in San Diego, California, the long-established company has been providing weighing solutions and packaging equipment for a variety of industries including food processing, automated manufacturing, chemicals, plastics, rubber and more over the past 100 years.
Hardy assists processors and manufacturers by offering solutions that create a drastic reduction in waste while enhancing quality and productivity by as much as 50% over other industrial weighing and packaging equipment. Hardy’s goal is to provide high performance weighing equipment at the least total cost to own. This is why the ISO 9001:2015 certified industrial scale company stays on the pulse of innovations in the field. Their extensive product range comprises accurate industrial weighing scales, including floor scales, load cells, platform scales, weight modules, weight controllers and more.
Hardy Process Solutions is an Encompass Global Partner with Rockwell Automation. The high-quality weighing modules and controllers of our US partner are developed in collaboration with Rockwell and are thus optimally tailored to Rockwell systems.
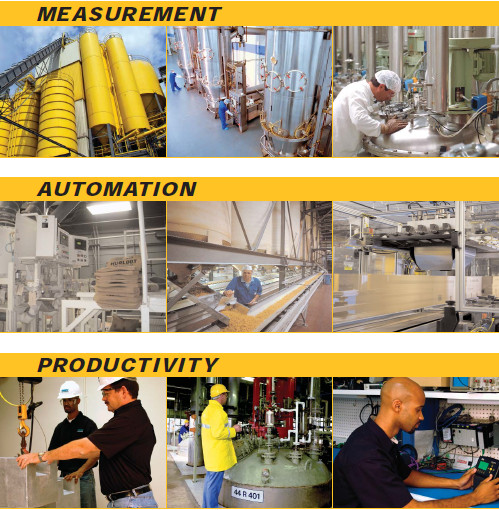
Equipped with the “Hardy Process Toolbox” – a unique set of productivity tools that support industrial weighing functions – Hardy instruments provide valuable assistance in commissioning, maintenance and fault location. Each tool saves time, increases accuracy, improves efficiency or reduces risk in process weighing applications, while saving OEMs considerable development and system integration time.
Our customers such as Mars, Royal Canin and Goodyear are convinced by the particular benefits:
- Practical: the fast and simple C2 Electronic Calibration without the need for test weights
- Stable: the automatic vibration suppression (WaverSaver)
- Secured: settings and adjustment data are securely stored for back-up and transfer (Secure Memory Module)
- Networked: the integrated web server enables remote access and setup of the instruments via Ethernet (Embedded Web Server)
- Built-in support: Hardy instruments are equipped with a powerful diagnostic and troubleshooting feature (Integrated Technician)
- Active support: for planning, installation and operation of the Hardy devices, our competent B+L support is always at your side.
Hardy’s process weighing solutions are easy-to-install, configure, commission and operate. They are easy-to-maintain and save you time, money, raw materials and/or finished product.
For process weighing applications, we offer a selection of suitable Hardy solutions here:
PLC Weighing Modules
Plug-in Weigh Scale Modules for ROCKWELL PLC
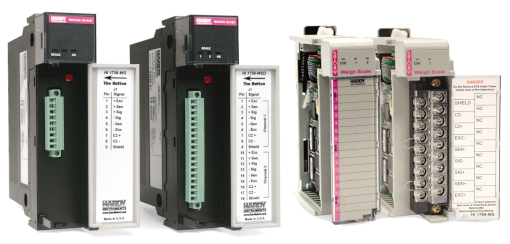
HI 1756-WS and -2WS – Single and Dual ControlLogix® Weigh Scale Modules
HI 1769-WS and -2WS CompactLogix® Modules – Small size, high performance!
Hardy’s HI 1756-WS is available as a single slot, single or dual (-2WS) weigh scale module that mounts in Rockwell®ControlLogix® Chassis.
Hardy’s compact weigh scale module HI 1769-WS is available in single or dual channel models for use in Rockwell® CompactLogix® PLC controllers (and certain MicroLogix™1500).
These PLC weighing modules read and condition weight and diagnostic data from one set or two separate sets of strain gauge load sensors or load cells and communicate this data over the I/O chassis backplane to the PLC processor. Both modules reduce installation costs, as they do not require an external Ethernet switch or router.
Hardy Process Solutions is an Encompass Global Partner with Rockwell Automation, which ensures a smooth workflow with their equipment.
Special features
- Single or dual scale plug-in modules
- C2 Electronic Calibration, fast and simple without test weights
- Waversaver, automatic vibration suppression for stable, accurate weight readings
- IT (Integrated Technician), integrated support tool for troubleshooting and diagnostics
- Super easy and seamless integration with
Rockwell Add-On-Profiles (AOP), Rockwell Automation configuration files,
Rockwell Faceplates/AOIs for HMIs, SE and ME software instruction tags,
Direct Backplane Connectivity
Applications
- Batching / Blending
- Filling / Dispensing
- Level-by-Weight
- Check Weighing
HI 1734-WS Point I/O
The Hardy HI 1734-WS Point I/O Series Weight Processing Module is an ultra-compact plug-in module for Rockwell’s Point I/O chassis
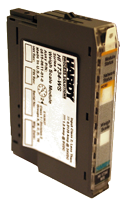
The HI 1734-WS is a true weight processing module, compared to competitive offerings that merely pass weight data through to the PLC for interpretation. It also will have a Rockwell Add-On-Profile (AOP) that will automatically recognize the module when it is plugged into the Point I/O chassis.
The Hardy HI 1734-WS module is ideal for POINT I/O applications where fast, stable weight data and low-cost of ownership are critical components to successful machine and process design. Designed exclusively for weight processing, the HI 1734-WS enhances productivity of manufacturing systems by digitally suppressing noise and dramatically reducing scale settling time.
Ultra-compact at just a ½” wide, the HI 1734-WS module saves cabinet space over the use of dedicated instrumentation, reducing both machine cost and control cabinet footprint.
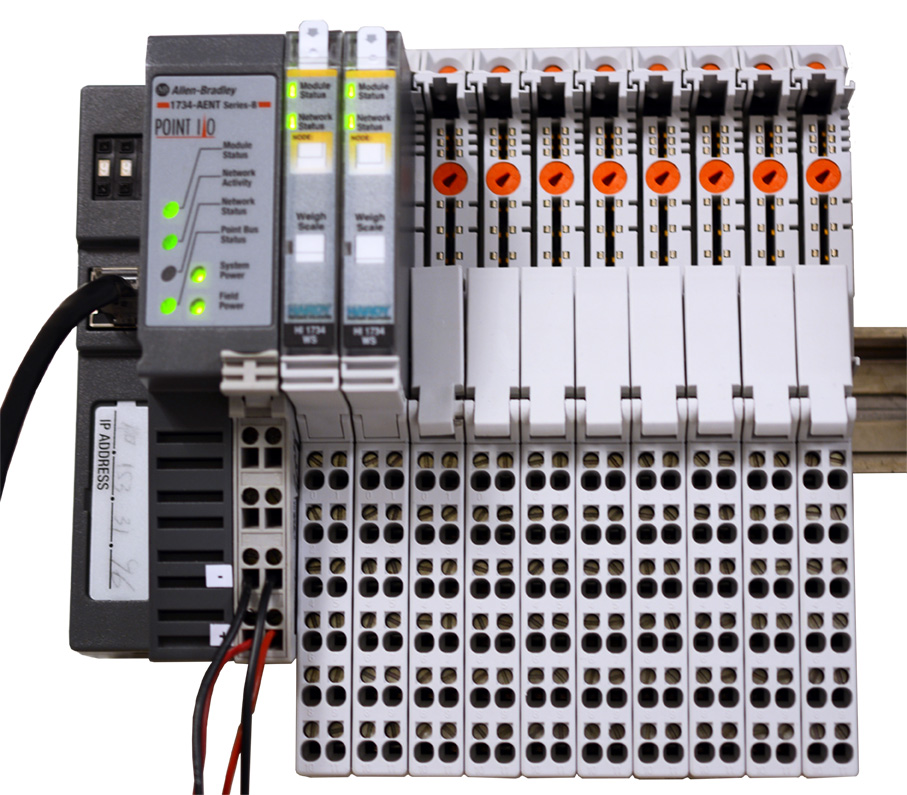
Special features
- New plug-in module for Rockwell Point I/O
- Ultra-compact, only a 1/2″ wide
- Hot-swap, can be inserted and removed under power
- C2 Electronic Calibration, fast and simple without test weights
- Waversaver, automatic vibration suppression for stable, accurate weight readings
- IT (Integrated Technician), integrated support tool for troubleshooting and diagnostics
- Super easy and seamless integration with
Rockwell Add-On-Profile (AOP), Rockwell Automation configuration files,
Rockwell Faceplates/AOIs for HMIs, SE and ME software instruction tags
Applications
- Inventory Measurement
- Level Measurement
- Batching / Blending
- Filling / Dispensing / Dosing
HI 6600 Modular Sensor System
Revolutionary concept for process weighing technology:
Up to 30 Channels of Weight on one SINGLE Ethernet Connection!
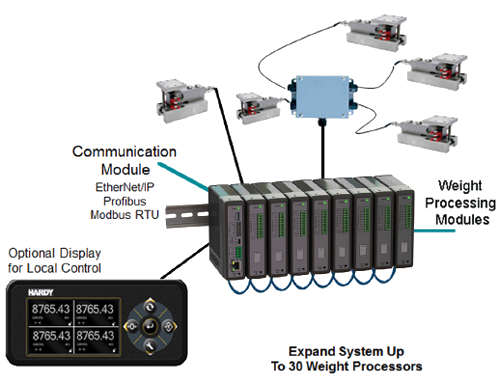
The HI 6600 series is a modular system of weight processors that deliver up to 30 channels of fast, stable, high-resolution weight readings to PLCs, PACs and DSCs over a single fieldbus network connection.
Ideal for applications that require more than one channel of weight, such as inventory tank farms, batching systems and multi-head filling machinery; each channel of the HI 6600 processes signals from up to four connected load cells then outputs the entire system’s weight data over Ethernet TCP/IP, Modbus TCP or RTU, and either EtherNet/IP or Profibus-DP, depending on the Hardy Gateway Module.
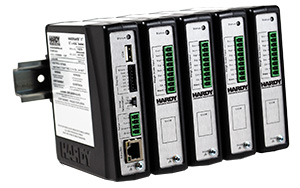
SOLID PERFORMANCE
The HI 6600 enhances productivity of manufacturing systems by digitally suppressing noise and dramatically reducing scale settling time. Even in noisy environments with excessive amounts of mechanical vibration, the HI 6600 provides a steady 1:10,000 resolution in oz, lb, ton, g, and kg with 110 updates per second over its variety of communications protocols.
EASY INSTALLATION
Just snap the number of weight channels you need onto a DIN rail, connect power, cable the units together to the Gateway Module using standard Cat5e cable, connect sensors, power up and press DISCOVER. The system will automatically identify all the modules connected together and make them addressable for set-up and calibration through the PLC, embedded Webserver or optional display. A Rockwell EDS_AOP simplifies integration using RSLogix.
Special features
- Modular multi-channel system with up to 30 weight processors and a gateway module
- Optional display, can show weight from up to 30 connected weight modules, displaying up to 4 channels simultaneously
- Ultra-low power consumption eliminates the cost of cooling in the control cabinet
- EtherNet/IP, Ethernet TCP/IP, Modbus TCP or RTU, or Profibus-DP
- Embedded Web Server, enables remote access to setup and calibration from anywhere on your Ethernet network
- C2 Electronic Calibration, fast and simple without test weights
- Waversaver, automatic vibration suppression for stable, accurate weight readings
- IT (Integrated Technician), integrated support tool for troubleshooting and diagnostics
- Easy installation and setup, with Rockwell EDS_Add-On-Profile
Applications
- Inventory Measurement
- Level Measurement
- Batching / Blending
- Filling / Dispensing / Dosing
HI 6500 and HI 6500-XP
Weight Processors
Process Weighing Made Easy:
Weight Processors Now Include Extreme Weight Processor Version with 6X the Speed and 3X the Resolution
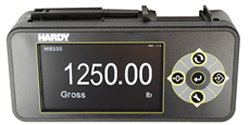
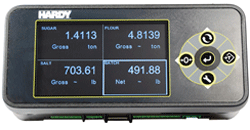
The HI 6500 series are EtherNet/IP® enabled weight processors with a Rockwell Add-On-Profile (AOP) and Faceplate/AOIs. They have a big, bright multi-channel display and deliver fast, high-resolution weight readings. They also feature Profibus-DP, Modbus, Analog, and Ethernet communication options.
Weight processors are used as front ends to control systems or standalone for all types of general weighing applications. Operating blind or with a display, they measure, condition and communicate weight without any need to control.
SOLID PERFORMANCEThe HI 6500 series delivers stable processed weight with a resolution of 1:10,000 and an update speed of 110 updates per second (processor, display and communications). They enhance the productivity of process manufacturing systems where fast, precise weight-based controls are critical.
EXTREME WEIGHT PROCESSOR
The HI 6500-XP Extreme Weight Processor can process and output 660 updates per second of processed (stable) weight with a resolution of 1:30,000. The HI 6500-XP represents the state-of-the-art in processing uniformity and speed. A/D conversion, weight processing and the communications port ALL update at 660 times per second, providing the PLC with the latest processed weight reading every 1.5 milliseconds. Many competitor’s products execute the A/D conversion at one frequency, then process the weight and communications ports at a much slower rate typically 20 to 50Hz, only providing the PLC with an update every 20 to 50 milliseconds. The HI 6500-XP results in better product consistency and product yields while reducing processing time, waste time and materials. It is designed for applications where speed and accuracy are paramount to control and quality, and it’s ideal for high-speed filling, dispensing and check weighing, where materials are often fed and weighed in motion at high speeds.
INSTALLATION YOUR WAY
For panel mounting, simply drill five holes to mount the keypad/ display on the front and the instrument to the other side. For blind or remote mounting, just snap its built-in clip onto a DIN rail or mount on a wall. The HI 6500 series fits in a 2″ deep cabinet!
Special features
- Maximized speed and accuracy
- Optional multi-channel display, showing up to 4 instruments simultaneously
- EtherNet/IP, Ethernet TCP/IP, Modbus TCP or RTU, Profibus-DP and more communication options
- Embedded Web Server, enables remote access to setup and calibration from anywhere on your Ethernet network
- C2 Electronic Calibration, fast and simple without test weights
- Waversaver, automatic vibration suppression for stable, accurate weight readings
- IT (Integrated Technician), integrated support tool for troubleshooting and diagnostics
- Easy installation and setup, with
Rockwell Add-On-Profiles and HMI Faceplates/AOIs
Applications
- Inventory Measurement
- Level Measurement
- Batching / Blending
- Filling / Dispensing / Dosing
- Check Weighing
HI 4050+ Weight Controller
The fast, high-resolution HI 4050+ has proven itself over many years in process weighing applications. The instrument is scalable, easy to configure / operate and the SD memory card guarantees easy data transfer.

The HI 4050+ is a fast, high-resolution weight controller that helps to reduce your labor content, speed your production throughput, and improve the quality and safety of your end product. The HI 4050+ acts as a front end weight controller to a PLC, PC or DCS system. It also operates as a standalone weight controller or monitor.
FAST & STABLE WEIGHT READINGS
With a selectible update rate of 100 or 250 updates per second, WAVERSAVER conditioning and Hardy’s new WAVERSAVER+ patent pending adaptive filtering algorithms, the HI 4050+ displays accurate, stable rate readings fast. With a processed weight resolution of 1:30,000 and an addressable resolution of 1:100,000, the HI 4050+ is precise and accurate.
The HI 4050+ is easy to mount – not least thanks to the low installation depth of 3″ – and offers various installation options, e.g. panel-mount, with separate display or without display for DIN rail mounting.
Hardy Process Solutions is an Encompass Global Partner with Rockwell Automation, which ensures a smooth workflow with their equipment.
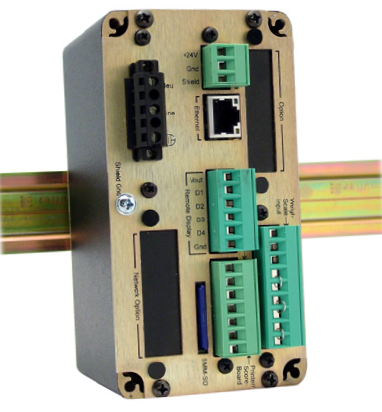
Special features
- Secure Digital Memory Module (SMM-SD) card, to automatically store configuration data, and easily transfer it from one weight controller to another
- Embedded Web Server, enables remote access to setup and calibration from anywhere on your Ethernet network
- C2 Electronic Calibration, fast and simple without test weights
- Waversaver, automatic vibration suppression for stable, accurate weight readings
- IT (Integrated Technician), integrated support tool for troubleshooting and diagnostics
- EtherNet/IP, DeviceNet, Modbus TCP & RTU, Analog, RIO, Profibus and more communication options
- Highly configurable, to suit your specific weighing application, e.g. with or without display, either AC or DC power, weight by rate, remote mount
- Easy installation and setup, with Rockwell Add-On-Profile
Applications
- Batching / Blending
- Filling / Dispensing
- Level-by-Weight
- Check Weighing
- Rate Monitoring
HI 4060 Loss-in-Weight Rate Controller
Hardy’s HI 4060 is a compact, single-feeder, closed-loop rate controller for use in a variety of applications, including auger, belt and vibratory-based feeders, converting them from volumetric to gravimetric.
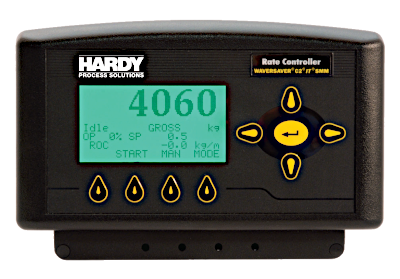
After supplying excitation to the load sensors and digitizing the weight signal, the rate controller provides an analog output to control the feeder speed and adjusts this signal based on the required rate at which the feeder is losing weight. The HI 4060 can communicate this information real-time to a PLC or a PC to control the entire process.
MULTIPLE FEEDER CONTROL
The HI 4060 is a powerful building block when it comes to multiple feeder systems. It can act as a master to multiple controllers or as a slave to other HI 4060’s or other process inputs.
The HI 4060 loss-in-weight rate controller features:
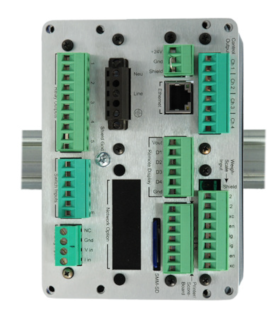
- Automatic closed loop control: continuously adjusts the feeder to deliver the desired feed rate
- True five-point automatic rate calibration: produces high feed accuracy for a wide range of feed rates
- Multiple configuration storage: stores hundreds of different system configurations
- Automatic feeder refill: starts and stops refilling without interrupting the feeding of material
- Convenient manual mode: allows manual speed control, with switch to automatic control at the touch of a button
- Various alarms, including rate tolerance and disturbance
- Graphics Display Mode: graphs actual feed rate vs. setpoint or operation percentage output
Special features
- Secure Digital Memory Module (SMM-SD) card, to automatically store configuration data, and easily transfer it from one instrument to another
- Embedded Web Server, enables remote access to setup and calibration from anywhere on your Ethernet network
- C2 Electronic Calibration, fast and simple without test weights
- Waversaver, automatic vibration suppression for stable, accurate weight readings
- IT (Integrated Technician), integrated support tool for troubleshooting and diagnostics
- Ethernet and optional DeviceNet, EtherNet/IP, Remote I/O, Profibus, Modbus TCP/IP, Analog
- Easy to install and configurable to suit your specific application
Applications
- Gravimetric Feeding
- Continuous and Batch Rate Control
- Master/Slave